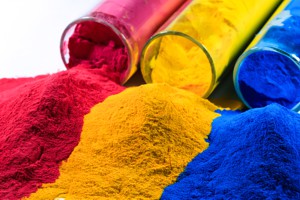
Quality metal fabricators across all industries are improving products by embracing powder-coating, but this type of coating also offers unique advantages for commercial signs. Powder-coating improves the aesthetics of your sign, while also ensuring long-term durability for both inside and outside signage.
While most sign companies simply spray paint the metal sign, we have shifted to powder-coating, and that's just one of many features that set our signs apart from the competition.
What is Powder-Coating?
Powder-coating is a process where a powder of resin and fine pigment particles are electrostatically sprayed onto metal. When the powder cures to the metal, the result is a durable, uniform finish that looks like paint but offers a host of additional advantages. There are two main types of powder-coating: thermoplastic and thermoset.
Thermoplastic powder-coating provides a corrosion-resistant coating, which can be re-melted and recycled. However, that also makes this type of coating more susceptible to damage from hot electronics or the sun.
Thermoset also resists corrosion, but this decorative and protective finish cannot be melted down. Once applied, thermoset powder-coatings are permanently set. The polymers in this coating cross-link during the curing process and create a permanent chemical bond with the underlying metal. This enhances the resistance to heat and chemicals, while also improving the structural integrity of the sign itself.
Additionally, thermoset powder-coating is more affordable than thermoplastic coating. Because of these key advantages, thermoset is the type of powder-coating used on Stewart Signs.
What is the Thermoset Powder Application Process?
Applying thermoset powder to metal signs is a relatively fast process. To get started, the fabrication technicians hang clean, cold sign metal from hooks on a rolling rack. Hanging the metal ensures that every single part can be hit with the spray, and the rolling rack allows technicians to move the sign from the spraying area to the curing oven without touching it or disrupting the coating.
Additionally, the rolling rack connects to a ground wire. Then, as the positively charged powder tries to ground itself, it attaches to the bare spots on the metal. By leveraging the laws of electricity, this application process helps to ensure a flawless and completely even powder-coating on the metal. There is no lumpy build-up because once the powder attaches to the metal, excess powder cannot find a place to stick - so, it simply falls to the ground.
Once the metal is completely covered, the sign goes into a curing oven. After about 15 to 20 minutes at 400 degrees Fahrenheit, the powder-coating liquefies and then cures to a hard and durable finish that is chemically fused to the metal.
After painting, thickness is checked to ensure consistency. Film thickness can affect the color, gloss, surface profile, adhesion, flexibility, impact resistance and hardness of the coating, and the fit of pieces assembled after coating can be affected when film thickness is not within tolerance. Powder-coating thickness may also affect the application's impact resistance, flexibility, hardness, edge coverage, chip resistance, weathering, resistance to salt spray, and ability to retain gloss.
When insufficient powder-coating is applied, it does not provide adequate coverage and protection. For example, metals require enough coating thickness for adequate protection from environmental effects such as corrosion (steel) or oxidation (aluminum). Additionally, inadequate powder-coating thickness may result in poor surface finish and undesirable appearance or color.
More about our powder-coating process:
-
Our powder-coat paint booths are 4002 ft.
-
We use aluminum oxide sand blast media
-
75-80% of blast media is recaptured, recirculated, and reused
-
Our cured paint thickness is 2-2.5 Mil
-
Our capacity is 1.5 complete integrated LED signs per hour
To ensure full coverage, we paint individual sign components, including the trim, cowling, sign cabinet, support structure, panels and other paintable accessories. Then, the individually painted components are assembled.
Powder-Coating Versus Spray Paint and Other Finishing Options
The difference in the application methods between spray painting and powder-coating leads to increased durability and resistance, which is why powder-coating is used on everything from heavy machinery to household appliances. Some of the main advantages include the following:
-
No scratches, chips, or fading — spray paint is very susceptible to chipping, but powder-coating resists these threats because the coating fuses with the metal.
-
Fewer maintenance issues than spray paint.
-
No touch-ups required — spray paint coating may require regular touch-ups to deal with chips and scratches.
-
Unlimited color options.
-
Variety of finishes available, including glossy, flat, clear, and others.
-
Multiple textures possible such as smooth, wrinkled, and rough.
-
No solvents used in the application process.
-
No volatile organic compounds (VOCs) emitted after application — in contrast, spray paint can emit a lot of VOCs.
-
Perfectly even and uniform coating process allows you to add a thicker coat than paint, without sagging or wrinkling.
-
Lower overhead costs in the production process — powder-coating plants don't need as much equipment, and they have relaxed safety standards compared to facilities that use coating options associated with VOCs or other off-gassing chemicals.
We are always trying to find new ways to improve the quality of signs we provide to our clients, and powder-coating is just one of the ways our signs stand above the competition. To learn more about the benefits of powder-coating or to get a custom quote, contact us today.